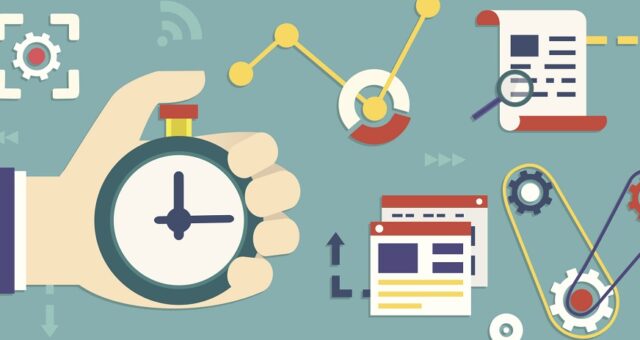
Need of the Hour !! – Overall Equipment Effectiveness (OEE)
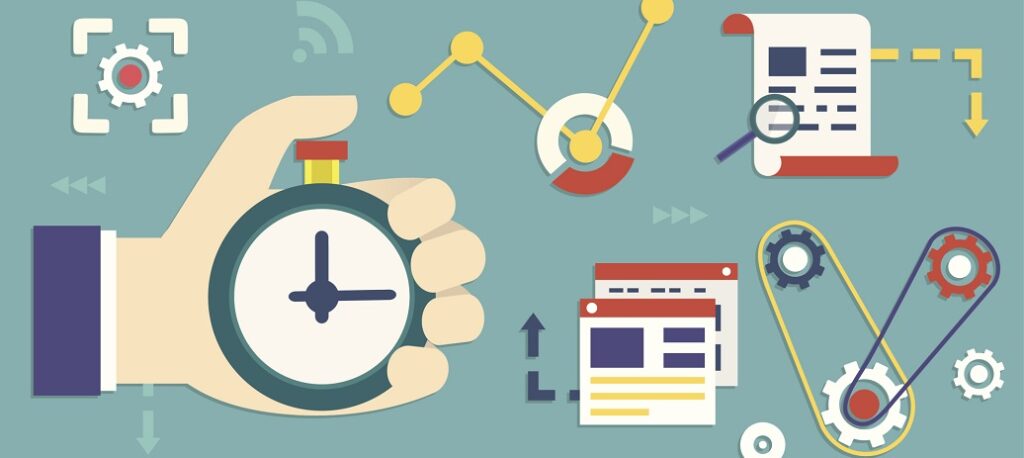
Out of all the prevailing industries, manufacturing seems to be one of the most challenging and interesting choice. Aspirations are set clear by Government of India to increase manufacturing sector contribution to 25% of GDP by 2022. One commendable measure taken towards this goal is “Make in India” program that has a great impact internationally after its launch. Until 2018 the Gross Value Added (GVA) of manufacturing sector was at peaks touching 390 Billion US dollars. Among which the automotive sector contributes to almost 20% of the goods flow in the market. Thereby becoming the leading sector among the other manufacturing sectors in India.
Being such a competitive field with huge market size there ought to be definite challenges. Understanding the complexities involved will surely help to survive better in this field. Most of the manufacturers face pricing pressures for the product. It is totally based on competitive pricing mode, therefore cost reductions becomes their priority. Reducing fixed costs and lowering the costs of goods sold (COGS) are the better ways to handle product pricing. One another major challenge comes to the table is in the area of Quality. Quality expenditure along with maintenance are itself becoming a critical cost adding factors.
There are three main challenges that exists most commonly. One is people or man power performance. It is the question of how efficient are they in contributing to production and how consistent are they in performing their responsibilities. The factor of value addition by the employees can also be analysed using man power performance measures. The second challenge can be due to Materials. It is ultimately the materials that are used to produce the product. The type of material directly affects the product performance. It is therefore important to question how far or how consistent is the material helping the product to be at its best. The third challenge of manufacturing is because of Machines or Equipment. The overall production capacity and quality are determined with the type of machines that are used. Therefore, machines decide on the output that has to be produced. In other words, how effective are the machines used to produce the maximum output?
Thus battling all the above becomes the core of challenges for all the manufacturers. Especially the third challenge of maintaining the performance of the machines to the expected mark is where the trick lies. The equipment efficiency is what manufacturers target primarily to bring their overall productivity to maximum. Concepts like Total Quality Management (TQM), Total Productive Maintenance (TPM), Lean Manufacturing and other management tools have helped in order as an industry to evolve.
“Measure what is measurable and what is not measurable make measurable” – Galileo Galili
It is believed that whatever is measured can be taken for further improvement. In the field of any manufacturing, the output matters. The output speaks on how efficient is their manufacturing process. In order to stay competitive, every single manufacturing unit considers their losses due to equipment or machines as a critical factor that decides their business. In order to know their efficiency, they need to know few operational losses. The trick lies on measuring those losses and gaining idea on optimizing their efficiency. This leads to the concept of OEE – Overall Equipment Effectiveness which is the need of the hour.
OEE is a mathematical calculation of how effective are the equipments or machines used and gives us the overall efficiency of the manufacturing process. It consists of three elements – Availability, performance and quality. OEE calculation considers all the above factors and gives the results in terms of percentage. If 100% is achieved it means that all the products are quickly produced with the best quality, without any stop failures.
OEE address to 6 Major Losses that are very critical to any manufacturing unit
FACTORS |
6 BIG LOSSES |
COMMENT |
AVAILABILITY |
UNPLANNED STOPS |
EQUIPMENT FAILURE |
PLANNED STOPS |
SETUP AND ADJUSTMENTS |
|
PERFORMANCE |
SMALL STOPS |
IDLING OR MINOR STOPS |
SLOW CYCLES |
REDUCED SPEED |
|
QUALITY LOSS |
PRODUCTION REJECTS |
PROCESS DEFECTS |
START UP REJECTS |
REDUCED YIELDS |
In addition, OEE adds the following advantages. So, What do you get?
- Major Losses according to TPM will be taken care.
- Allows you to monitor and improve your manufacturing efficiency
- ROI on equipment will be assured if applied
- Visualize and get the scope of further applying concepts such as I-IOT
- Achieve real time target and stay competitive in business
For Further Assistance Contact us
lean tool